Dip coating is a critical coating technique used in various industries. In this process, surface tension plays a key role in forming a uniform, high-quality coating. Proper control of surface tension can enhance product performance and appearance. This article covers the basics of surface tension in dip coating, control methods, and key considerations during the process.
Basics of Surface Tension in Dip Coating
What is Surface Tension?
Surface tension is the force that minimizes the surface area of a liquid. A water droplet forms a round shape due to surface tension. This force results from the difference between intermolecular attraction within the liquid and the attraction between liquid and air molecules. Surface tension varies depending on the type of liquid and its temperature.
Role of Surface Tension in Dip Coating
In dip coating, a workpiece is immersed in a coating liquid and then lifted to form a uniform film. During this process, surface tension plays a key role in determining how the coating liquid spreads on the workpiece and the final coating thickness. If the surface tension is too high, the liquid may not spread evenly, resulting in an inconsistent coating or dripping. On the other hand, if the surface tension is too low, the coating may become too thin or fail to form a uniform layer.
Relationship Between Surface Tension and Wettability
Surface tension is closely related to the wettability of the workpiece. Wettability refers to how well a liquid makes contact with a solid surface. Poor wettability prevents the coating liquid from spreading evenly, making it difficult to form a uniform film. By controlling surface tension, wettability can be improved, ensuring consistent coating formation.
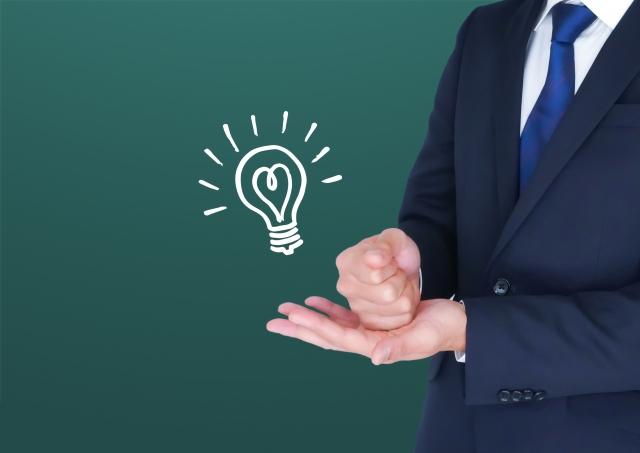
Controlling and Improving Surface Tension in Dip Coating
Enhancing Wettability Through Surface Modification
Surface treatment can improve wettability. Techniques such as UV exposure or plasma treatment enhance the hydrophilicity of the workpiece surface (the ability to attract and hold water), allowing better wettability of the coating liquid. This leads to more uniform film formation.
Controlling Surface Tension by Adjusting Coating Liquid Composition
Adjusting the composition of the coating liquid also allows control over surface tension. By adding additives or modifying the type and concentration of solvents, the optimal surface tension can be achieved.
Key Considerations in the Dip Coating Process
In dip coating, factors such as lifting speed and liquid temperature also affect coating thickness. Controlling these parameters properly ensures uniform thickness. Additionally, air bubbles in the coating liquid can cause coating defects, making their removal crucial.
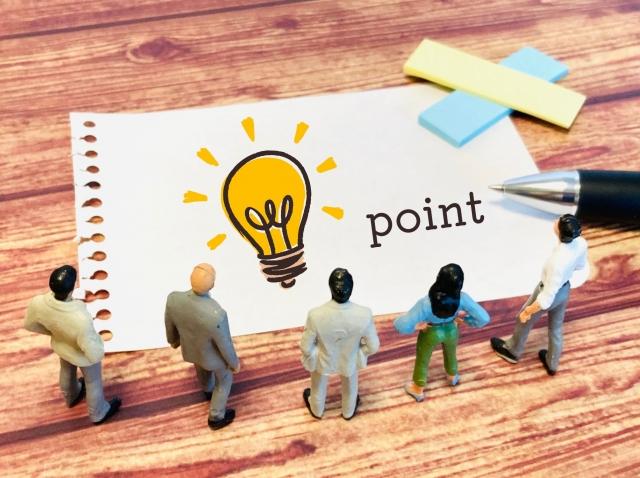
Summary
Surface tension in dip coating is an essential factor for achieving a uniform film. It is closely related to the wettability of the workpiece, and its control can be achieved by adjusting the coating liquid composition or modifying the workpiece surface.
Additionally, considering process factors such as lifting speed, liquid temperature, and air bubble removal contributes to high-quality dip coating. Proper control of surface tension is crucial for improving both the performance and appearance of the final product.
We encourage you to use the insights shared in this article to develop the optimal coating process.