Dip coating is an essential technique used for surface treatment in various products. However, achieving a uniform film thickness is challenging, and irregularities are a major issue. These irregularities directly impact product quality, making it crucial to understand their causes and implement appropriate countermeasures. This article explains the mechanisms behind dip coating irregularities and practical solutions to mitigate them.
Understanding the Causes of Dip Coating Irregularities
Liquid Viscosity and Uniformity
Liquid viscosity significantly affects dip coating thickness and uniformity. If the viscosity is too high, the liquid does not adhere evenly, leading to irregularities. If the viscosity is too low, the liquid flows off too quickly, resulting in a thin coating. Maintaining a consistent viscosity through temperature control and ensuring proper mixing is essential for achieving a uniform coating. It is important to keep the coating liquid well-mixed so that its components spread evenly. If the liquid is not stirred enough, it can cause uneven coating thickness.
Lifting Speed and Coating Thickness Control
The lifting speed is a crucial parameter directly affecting coating thickness. Generally, a slower lifting speed results in a thinner coating, while a faster speed creates a thicker coating. However, this relationship also depends on factors such as liquid viscosity and surface tension. The optimal lifting speed varies based on the liquid properties and the desired coating thickness. Experimentation is necessary to determine the best speed for a given coating application.
Effect of Surface Tension and Wettability
The surface tension of the coating liquid and the wettability of the coated object affect how well the liquid spreads, influencing the occurrence of irregularities. If surface tension is too high, the liquid may bead up, making it difficult to form a uniform coating. Improving the wettability of the surface of a workpiece through pre-treatment can help the liquid spread more evenly and reduce irregularities.
Uneven Drying During the Coating Process
Irregularities can also occur during the drying process. If the drying temperature, airflow, or drying time is not properly controlled, cracks, pinholes, or uneven coating thickness may develop. Optimizing drying conditions helps prevent these issues.
Irregularities Due to Insufficient Stirring
If the coating liquid is not stirred properly, its components may separate, leading to uneven coating thickness. This is especially critical for high-viscosity liquids or those containing solid particles. Regular stirring and selecting the right mixing equipment are essential for maintaining coating consistency.
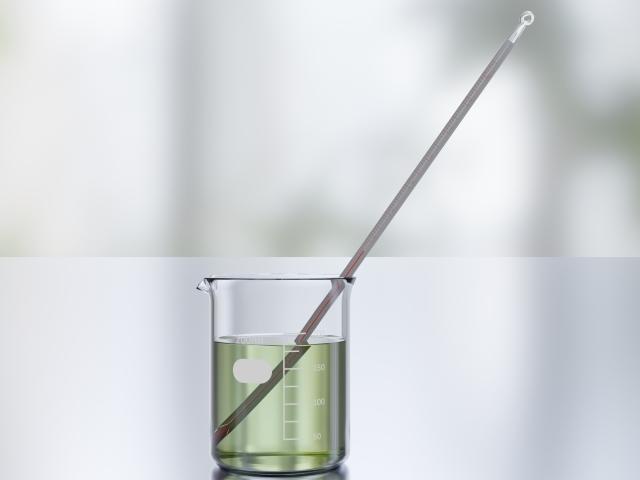
Effective Measures to Prevent Dip Coating Irregularities
Proper Liquid Preparation and Management
To prevent irregularities, proper preparation and management of the coating liquid are essential. It is necessary to carefully select materials, determine appropriate mixing ratios, use proper dissolution methods, and conduct thorough filtration. Additionally, it is crucial to continuously monitor the liquid’s condition, checking for viscosity stability and uniformity in composition.
Setting the Optimal Lifting Speed
As mentioned earlier, lifting speed greatly affects coating thickness. The optimal speed should be determined through experiments, considering the coated object, liquid properties, and desired thickness.
Importance and Methods of Pre-Treatment
Pre-treating the coated object is vital for improving liquid wettability and adhesion, which prevents irregularities. Proper pre-treatment, including cleaning, degreasing, and surface modification, enhances coating uniformity.
Optimizing Drying Conditions
Drying conditions significantly impact coating quality. Adjusting parameters such as drying temperature, time, and airflow is necessary to achieve optimal conditions. Inadequate drying may result in residual solvents, leading to reduced coating strength and irregularities.
Equipment Maintenance and Improvement
Proper maintenance of dip coating equipment is essential for preventing irregularities. Regular cleaning, part replacements, and inspections help maintain equipment performance and ensure stable coating results. If necessary, equipment improvements can enable better process control.
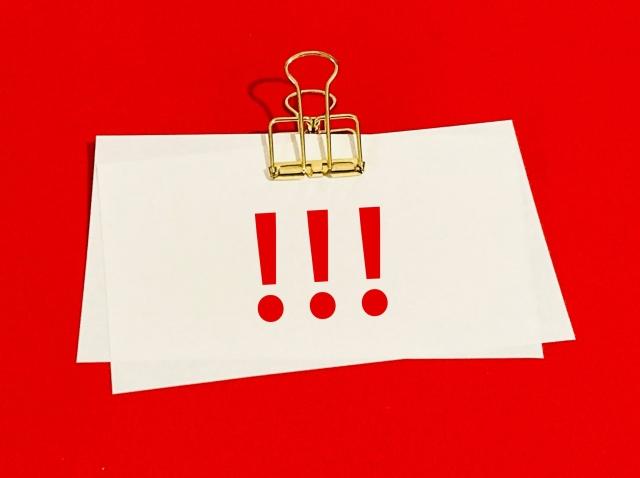
Summary
Dip coating irregularities result from complex interactions of viscosity, lifting speed, surface tension, drying, and stirring. Preventing defects requires understanding these factors and applying proper countermeasures. Key strategies include optimizing liquid preparation, pre-treatment, lifting speed, drying conditions, and equipment maintenance.
By applying the strategies discussed in this article, you can aim for a uniform and defect-free coating process.