Dip coating is a method in which a workpiece is immersed in a coating liquid and then lifted to form a uniform layer. This article introduces key points for ensuring a smooth dip coating process. It
also explains common issues that arise during dip coating and specific measures to address them.
In-Depth Guide to Key Considerations in Dip Coating
Challenges in Achieving Uniform Coating Thickness
Lifting speed is crucial in achieving uniform coating thickness in dip coating. If the speed is too fast, the coating becomes too thick, and if too slow, the coating becomes too thin, leading to inconsistencies. The optimal speed varies depending on the type of coating liquid, viscosity, temperature, and the material and shape of the workpiece.
In addition, conducting experiments to determine the best lifting speed is essential. For complex-shaped workpieces, liquid dripping and pooling are common, making it difficult to maintain uniform thickness. If uniformity cannot be achieved, using a linear lifting process (starting at a high speed and gradually slowing down) can be an effective solution.
Selecting the Right Coating Material and Ensuring Compatibility
Choosing the right coating liquid requires considering the desired thickness, characteristics, and compatibility with the workpiece. High-viscosity coatings or low-volatility solvents can cause dripping and uneven drying, requiring careful handling. Additionally, the compatibility of the coating liquid with the workpiece material is essential. Conducting pre-tests is crucial in selecting the most suitable coating liquid.
Key Considerations for the Drying Process
Controlling environmental conditions such as temperature, humidity, and airflow is essential during the drying process. Excessively high temperatures can cause cracks in the coating, while low temperatures may prolong drying time. High humidity levels can lead to poor drying results. Drying time varies based on the type of coating liquid and coating thickness, so setting optimal drying conditions is critical.
Challenges in Coating Complex Shapes
Applying dip coating to complex-shaped workpieces is challenging due to difficulties in achieving uniform thickness. Liquid pooling may occur in recessed areas, while raised sections may not receive enough coating. To address these issues, adjusting the workpiece angle or applying dip coating multiple times may be necessary.
Effects of Environmental Conditions and Countermeasures
Environmental conditions such as temperature and humidity affect the viscosity of the coating liquid and drying speed. In environments with significant fluctuations in temperature or humidity, maintaining uniform coating thickness can be difficult. Implementing measures to keep these factors stable is essential for achieving consistent results.
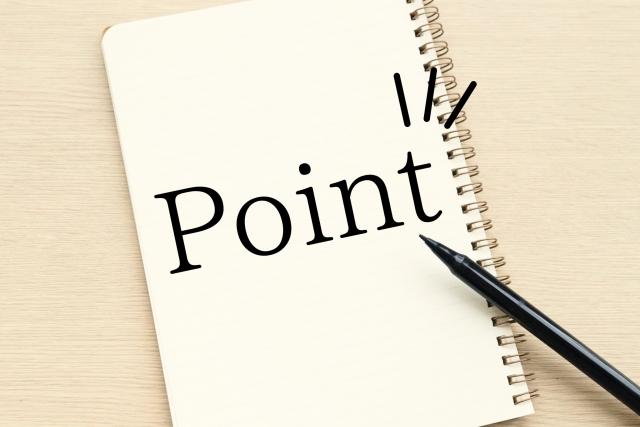
Key Factors for Successful Dip Coating
Importance of Proper Surface Preparation
Before dip coating, proper cleaning and surface preparation of the workpiece are crucial.
If dirt or oil remains, adhesion between the coating and the surface decreases, making the coating prone to peeling. Selecting the appropriate cleaning method and ensuring a clean surface will help achieve a high-quality coating.
Setting the Optimal Lifting Speed
As mentioned earlier, lifting speed has a significant impact on coating thickness. It is important to determine the optimal speed based on the type of coating liquid and the shape of the workpiece. Conducting experiments to find the best speed is recommended.
Managing Coating Liquid Viscosity
The viscosity of the coating liquid affects both thickness and uniformity. Using a coating liquid with the appropriate viscosity and managing temperature properly ensures stable coating results.
Quality Control and Inspection Methods
After coating, quality control is necessary to check for uniform thickness, appearance, and adhesion.
Choosing the right inspection methods ensures consistent quality.
Troubleshooting and Solutions
Issues such as uneven coating thickness, pinholes, and cracks may occur in dip coating. When these problems arise, it is essential to identify the cause and apply appropriate solutions.
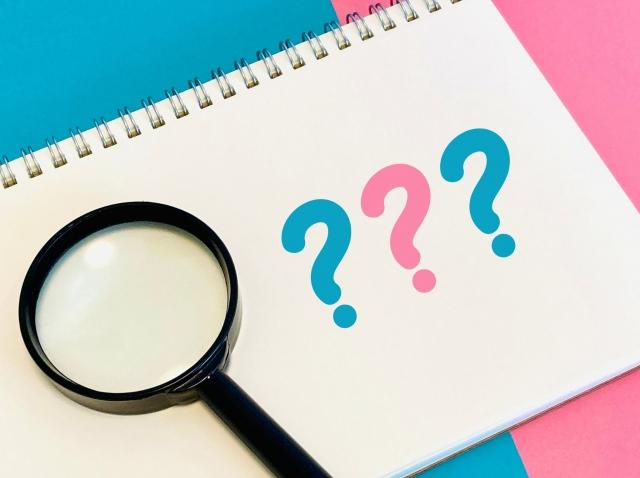
Summary
Dip coating is a simple yet highly effective coating method that requires careful attention to coating thickness uniformity and drying processes. By considering factors such as workpiece material, shape, and coating liquid properties, better coating results can be achieved. Proper surface preparation, optimal lifting speed, viscosity control, and environmental condition management are key to success.
Ongoing quality control and quick troubleshooting are also crucial for maintaining high coating standards.