Dip coating is widely used as a surface treatment technology in manufacturing. Its ease of operation and ability to achieve uniform coatings make it valuable across various industries. However, understanding its principles, coating thickness control, and applications requires technical knowledge. This article provides a clear explanation of the basics, applications, benefits, and drawbacks of dip coating.
Basics and Principles of Dip Coating
What is Dip Coating?
Dip coating is a coating technique in which a workpiece is immersed in a liquid and then lifted to form a uniform coating on its surface. This method effectively utilizes surface tension, gravity, and lifting speed to control the amount of liquid adhering to the workpiece and adjust the coating thickness. Its ease of operation and ability to achieve relatively uniform thickness make it a widely used technique.
Process and Mechanism of Dip Coating
The dip coating process consists of three main steps: immersion, lifting, and drying/curing. First, the workpiece is immersed vertically in the coating liquid. After a set duration, it is slowly lifted, with lifting speed significantly impacting coating thickness. Following lifting, the coating undergoes post-treatment processes such as drying or firing to harden the coating layer. These post-processing steps vary depending on the type of coating material and the required coating properties.
Key Factors and Considerations in Coating Thickness Control
Controlling coating thickness is a crucial aspect of dip coating. Thickness is determined by three key parameters: viscosity, density of the coating liquid, and lifting speed. Higher viscosity or density, as well as faster lifting speeds, result in a thicker coating. However, when adjusting these parameters, the coating liquid’s properties and the workpiece shape must be considered. Uneven thickness or pinholes may occur, making it essential to find the optimal balance of parameters.
Benefits and Drawbacks of Dip Coating
The benefits of dip coating include ease of operation, high productivity, simultaneous coating of both sides, and adaptability to various workpiece shapes. However, some drawbacks include the need for advanced techniques to control coating thickness and the requirement for a large initial volume of coating liquid. Additionally, the choice of coating liquid and post-processing steps significantly affect coating quality, requiring careful consideration.
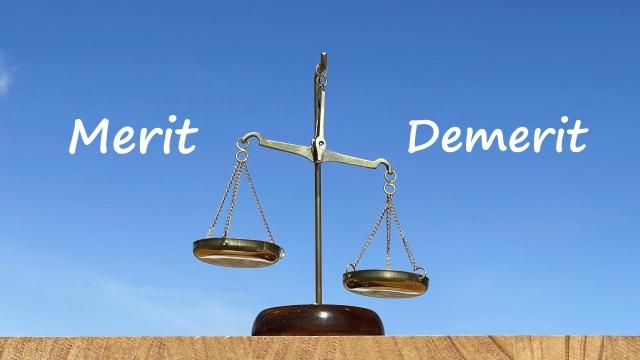
Applications and Future Prospects of Dip Coating
Applications in Various Fields
Dip coating is widely used in fields such as electronic components, optical parts, and medical devices.
For example, in electronics, it is used for forming protective coatings on circuit boards and improving solder wettability. In optics, it is applied to lenses and prisms to create anti-reflective coating.
In the medical field, it is used to apply biocompatible coatings to medical devices.
Future Potential and Challenges of Dip Coating
Dip coating is expected to become more advanced and diversified in the future. Research is progressing on nanometer-level coating thickness control and the development of new coating liquids. However, challenges such as reducing environmental impact and cutting costs still remain.
Comparison with Related Technologies
Dip coating is often compared to other coating technologies such as spray coating and spin coating. Each method differs in terms of applicable workpiece types, uniformity of coating thickness, and productivity. The most suitable technology depends on factors such as workpiece shape, material, and required coating quality.
Summary
This article explained the fundamentals of dip coating, its applications, benefits and drawbacks, and prospects. Dip coating is widely used for its ease of operation and uniform results, but precise thickness control and selecting the right coating liquid require advanced techniques. We hope this article has helped deepen your understanding of dip coating.