Dip coating is a simple coating technique widely used across various industries. This article explains the importance of thickness control in dip coating, practical techniques for achieving optimal thickness, and challenges along with their solutions.
Basics of Dip Coating and the Importance of Thickness Control
What is Dip Coating? Principles and Process
Dip coating involves immersing a material into a coating liquid and slowly lifting it to form an even layer on the surface. The thickness is influenced by factors such as immersion time, lifting speed, and the viscosity of the coating liquid. The balance between surface tension, gravity, and viscosity plays a crucial role in determining the final coating thickness.
Why Thickness Control is Important
Ensuring uniform coating thickness is essential for the success of dip coating. Uneven coatings can reduce performance, cause visual defects, or affect durability. For example, in optical applications, uniform thickness directly affects optical properties, while in anti-corrosion coatings, insufficient thickness reduces protection effectiveness.
Benefits of Uniform Coating Thickness
An even coating enhances functionality and durability. In optical applications, it improves light reflection and transmission, while in anti-corrosion treatments, it ensures a strong, protective layer against rust and wear. Additionally, a uniform coating improves the product’s overall appearance.

Techniques and Challenges in Thickness Control for Dip Coating
Factors Affecting Thickness Control
Several factors influence coating thickness. The key ones include:
- Lifting speed
- Coating liquid viscosity
- Temperature
- Surface condition of the workpiece
These factors interact with each other, making thickness control a complex process.
Lifting Speed and Its Impact on Thickness
Lifting speed directly affects the thickness of the coating. In general, faster lifting results in greater thickness, while slower lifting leads to a thinner coating. This happens because fast lifting retains more liquid, whereas slow lifting allows excess liquid to drain off.
The exact relationship between lifting speed and thickness depends on factors such as the viscosity, surface tension, and gravity of the coating liquid. It is often described using complex mathematical models rather than simple proportional relationships.
How to Adjust Coating Liquid Viscosity
The viscosity of the coating liquid plays a key role in determining thickness. Higher viscosity tends to produce greater thickness, while lower viscosity results in a thinner coating. Viscosity can be adjusted by changing the amount of solvent or adding thickeners. Choosing the right viscosity helps achieve the desired thickness efficiently. However, excessive viscosity can make uniform thickness difficult to achieve.
The Importance of Temperature Control
Temperature affects both viscosity and surface tension of the coating liquid, which impacts thickness. Higher temperatures lower viscosity, while lower temperatures increase it. Temperature fluctuations can also affect the stability of the coating liquid, making precise temperature control essential.
Other Influencing Factors and Solutions
Other factors, such as workpiece surface condition, ambient humidity, and aging of the coating liquid also impact thickness. Proper surface treatment, environmental control, and coating liquid management help minimize these effects.
Challenges and Solutions in Dip Coating Thickness Control
Some major challenges in dip coating thickness control include achieving uniform thickness on complex shapes, ensuring repeatability, and controlling precise thickness. Effective solutions include developing precision lifting mechanisms, optimizing coating liquid formulations, and strictly managing process conditions.
Advanced Thickness Control Technologies
Advanced techniques for thickness control include real-time thickness measurement systems and AI-driven process optimization. These technologies enable greater precision and reproducible thickness control.
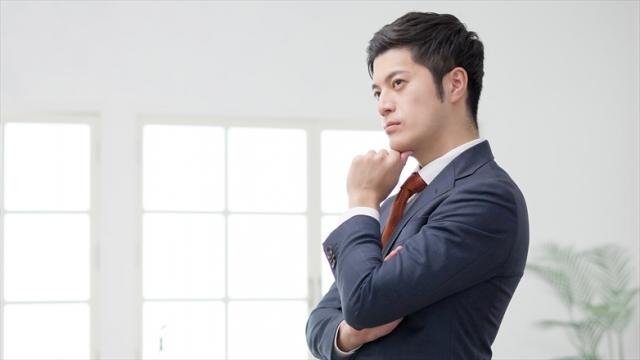
Summary
In this article, we discussed the importance of thickness control in dip coating, specific techniques for achieving it, and related challenges and solutions. Proper management of lifting speed, viscosity, and temperature ensures the desired thickness and uniformity.
However, these parameters interact in complex ways, making experimentation and trial-and-error essential for finding optimal conditions. With the use of advanced technologies, more precise thickness control can be realized. Thickness control is a crucial factor for the success of dip coating, and mastering its principles and techniques greatly contributes to improving product quality.
We hope this article proves helpful to engineers and professionals involved in dip coating technology.