Dip coating is widely used in manufacturing as a technique for forming uniform thin films on various materials. However, applying it to complex shapes presents significant challenges in ensuring uniform thickness.
This article explains dip coating principles, challenges in coating complex shapes, and future technological prospects.
Basics and Principles of Dip Coating
What is Dip Coating?
Dip coating is a method where a workpiece is immersed in a coating liquid and then lifted at a controlled speed to form a uniform coating thickness on its surface. Because the workpiece is submerged, both sides can be coated simultaneously. Additionally, depending on the properties of the liquid, dip coating tends to conform relatively well to complex shapes.
Conditions for Achieving Uniform Coating Thickness
To achieve uniform coating thickness, adjusting the viscosity of the liquid and the lifting speed is crucial.
In general, a faster lifting speed results in a thicker coating, while a slower speed produces a thinner coating. However, this is only a general guideline, as various factors such as liquid viscosity, surface tension, and the material of the workpiece also affect coating thickness.
Relationship Between Liquid Viscosity and Lifting Speed
Higher viscosity results in a thicker coating even at the same lifting speed. Conversely, lower viscosity leads to a thinner coating. Therefore, the viscosity of the coating liquid and the lifting speed must be carefully balanced to achieve the desired coating thickness.
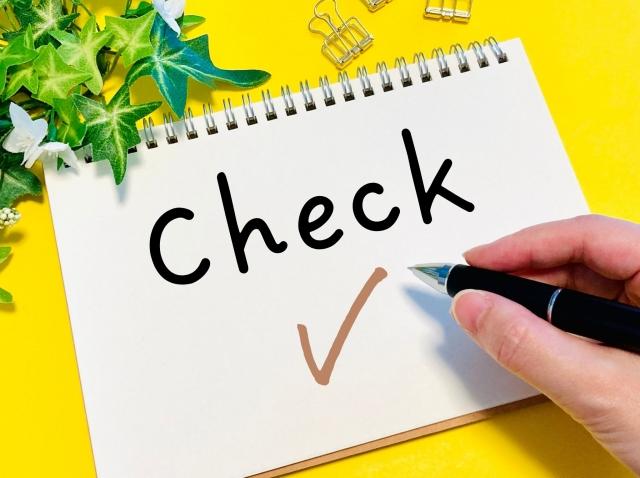
Applying Dip Coating to Complex Shapes: Challenges and Solutions
Challenges in Coating Complex Shapes
Coating complex-shaped workpieces presents challenges such as liquid pooling, air entrapment, and uneven drainage, making it difficult to achieve uniform coating thickness. In particular, workpieces with deep grooves or long, narrow shapes are more likely to exhibit variations in coating thickness.
Techniques for Adapting to Complex Shapes
A useful approach to addressing complex shapes is the “linear lifting process.” In this method, the lifting speed starts fast and then gradually slows down. This helps control the liquid flow more effectively and ensures uniform coating thickness. Additionally, adjusting the workpiece angle during immersion and lifting can help prevent air entrapment and liquid pooling.
Considerations for Dip Coating Complex Shapes
Selecting the right coating liquid is crucial when dip coating complex shapes. High-boiling-point solvents or water-based solvents evaporate more slowly, making them prone to dripping and uneven coating thickness. Therefore, setting appropriate coating conditions based on the workpiece shape and coating liquid properties is essential
Future Prospects for Technological Advancements
Dip coating technology needs to meet demands for higher precision and efficiency across various industries. Future innovations may improve adaptability to complex shapes, fine pattern formation, energy efficiency, and environmental sustainability.
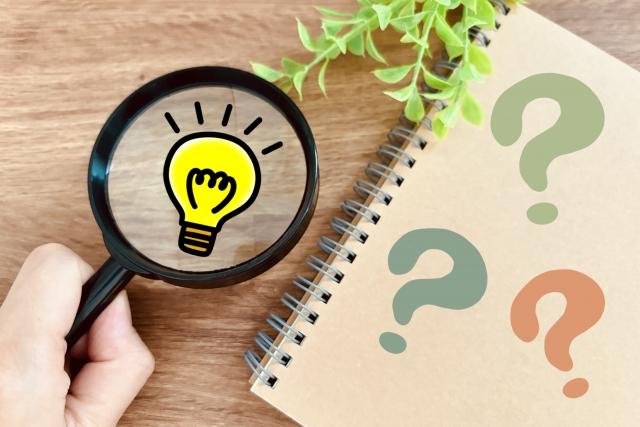
Summary
This article discussed the fundamentals of dip coating and challenges associated with complex shapes. Key factors such as adjusting liquid viscosity and lifting speed, employing linear lifting processes, optimizing workpiece angles, and selecting appropriate liquids are essential for achieving uniform coating thickness.
Coating complex shapes requires advanced technology and expertise. Mastering these techniques enables higher-quality coatings. Future advancements will further improve thickness control and adaptability to complex shapes.
Dip coating will continue to play a crucial role in various industries in the future.