ディップコーティングは、様々な素材への均一な薄膜形成を可能にする技術として、製造現場で広く活用されています。
複雑な形状のワークへの適用は、均一な膜厚を確保する上で大きな課題となります。
今回は、ディップコーティングの基本原理から、複雑形状への適用における工夫や注意点、そして今後の技術革新への展望までを解説します。
ディップコートの基本と原理
ディップコーティングとは何か?
ディップコーティングとは、ワークを液中に浸漬した後、一定速度で引き上げることで、ワーク表面に均一な膜を形成するコーティング方法です。
液中に浸漬させるため、ワークの両面に同時にコーティングできます。
また、液の特性にもよりますが、複雑な形状にも比較的追従しやすいという特徴があります。
均一な膜厚を得るための条件
均一な膜厚を得るためには、液の粘度と引き上げ速度の調整が重要です。
一般的には、引き上げ速度が速いほど厚い膜が、遅いほど薄い膜が形成されます。
しかし、これはあくまで目安であり、実際には液の粘度、表面張力、ワークの材質など、様々な要因が膜厚に影響を与えます。
液の粘度と引き上げ速度の関係
液の粘度が高いほど、同じ引き上げ速度でも厚い膜が形成されます。
逆に、粘度が低い場合は薄い膜になります。
そのため、目的の膜厚に応じて、液の粘度と引き上げ速度を最適なバランスで調整する必要があります。
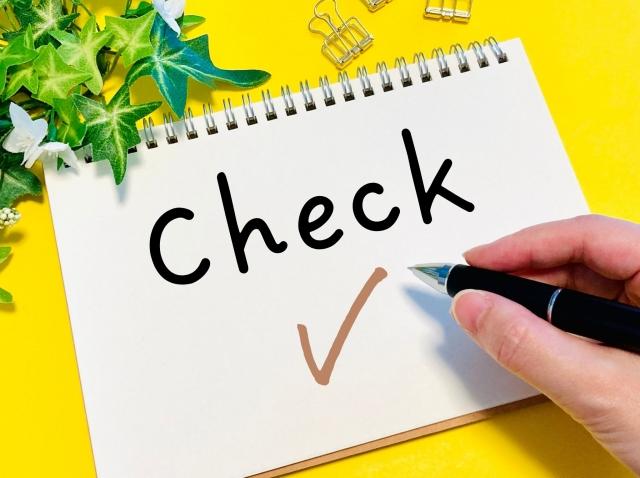
ディップコート複雑形状への適用と課題
複雑形状ワークへのコーティングの難しさ
複雑な形状のワークでは、液の滞留や液切れ、エアーの巻き込みなどが発生しやすく、均一な膜厚を得ることが困難になります。
特に、凹凸が激しい形状や、細長い形状のワークでは、膜厚ムラが顕著になる可能性があります。
複雑形状に対応するための工夫
複雑形状への対応策として、引き上げ速度を調整する「リニア引き上げ処理」が有効です。
これは、引き上げ開始時の速度を速くし、徐々に速度を落とすことで、液の流動性を制御し、均一な膜厚を得る手法です。
また、ワークの角度を調整しながら浸漬・引き上げを行うことで、エアーの巻き込みや液溜まりを抑制することも可能です。
ディップコート複雑形状における注意点
複雑形状へのディップコーティングでは、液の選択も重要です。
沸点の高い溶剤や水系溶剤を使用する場合は、揮発しにくいため液だれを起こしやすく、膜厚ムラが発生しやすくなります。
そのため、ワーク形状や液の特性を考慮した適切なコーティング条件の設定が不可欠です。
今後の技術革新への展望
ディップコーティング技術は、様々な分野で更なる高精度化、高効率化が求められています。
例えば、より複雑な形状への対応、微細なパターン形成、省エネルギー化、環境負荷低減など、技術革新はこれからも続いていくでしょう。
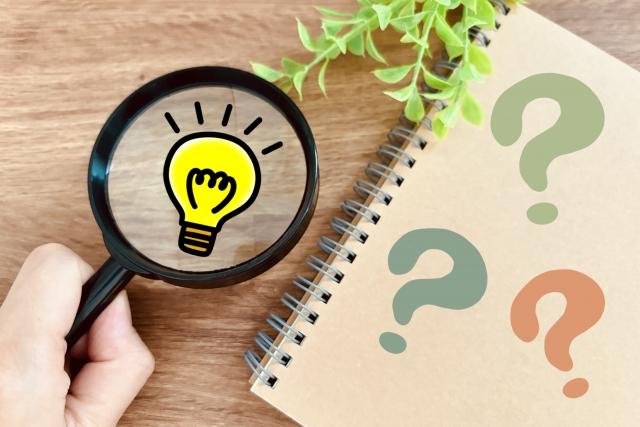
まとめ
今回は、ディップコーティングの基本原理と、複雑形状への適用における課題と対策について解説しました。
液の粘度と引き上げ速度の調整、リニア引き上げ処理、ワーク角度の調整、適切な液剤の選択などが、均一な膜厚を得る上で重要な要素となります。
複雑な形状への対応は、高度な技術とノウハウが必要ですが、これらの工夫を理解することで、より高品質なコーティングを実現できるでしょう。
今後の技術革新により、さらに複雑な形状への対応や、より高精度な膜厚制御が可能になることが期待されます。
ディップコーティングは、今後も様々な分野で重要な役割を果たし続けるでしょう。